Purifying of light and medium distillates.
The technology of lowering sulfur content in light and medium distillates is carried out by means of direct conversion of mercaptans in contact with catalyst surface.
Thanks to nanotechnological catalyst the oxidation process runs at more lower temperature in soft regime, that results in disulphide formation, but not oxides, that in hereinafter eases extracting sulfur containing components from the ready product. The worked out skeleton catalyst significantly exceeds usual in main parameters — segments of mesopores, that stipulates huge activity and spread surface of the material.
The skeleton base with driven on it by catalyst possessing high thermal and chemical resistance, with combination of ability to reverse oxidation and restoring, that stipulates its catalyst and photochemical properties.
Fundamentally technology of sweetening of hydrocarbon feed stock was taken direct soft catalyst oxiditing mercaptans directly in gas and liquid or gas throughflow in processes of primary run-down. Process of sweetening of throughflow carries out by transmission of throughflow of hydrocarbon aerosol (gas) through catalyst unit, with consecutive selective extraction of sulfur containing additions to the alkaline condition [Pic. №1, Pic. №2]. For extraction is used 5% of the size of purifying feed stock 1% alkali liquor, that is used multiplex. In comparison with process Merox economy of alcali makes 70-95%.
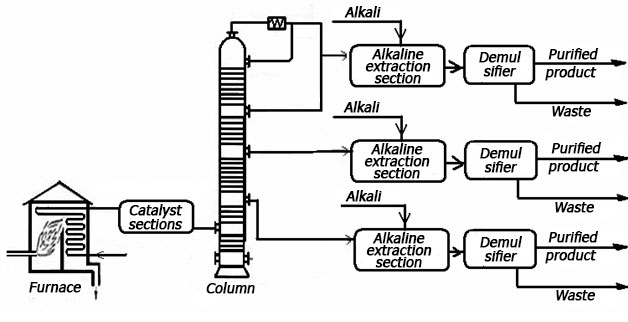
Picture №1. Principal scheme of technological process.
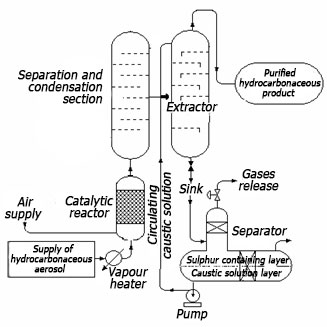
Picture №2. Technological scheme of sweetening installation.
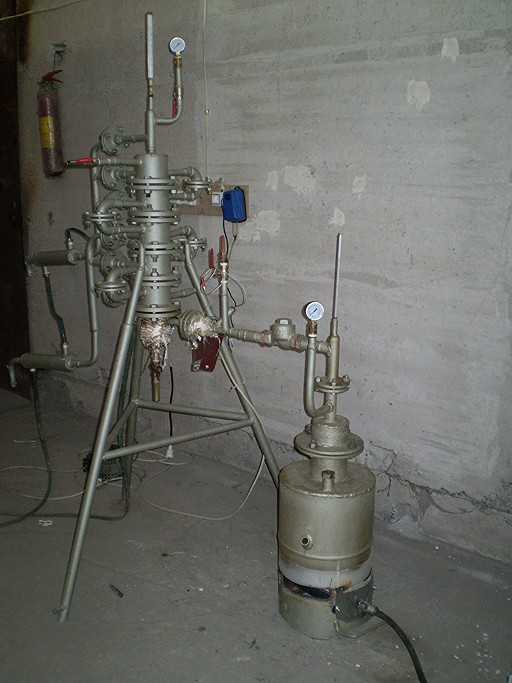
Picture №3. Pilot installation
This technology was tested in the pilot installation [Picture. №3].
The received data on some products sweetening are given in boxes. The definition of sulfur was done according following methodics:
1. Methodics of determination mass segment of total sulfur by titrimetry method based on restoring total sulfur on Raney nickel upto nickel sulphide, that solves by solution of hydrochloric acid. Segregated hydrogen sulphide is titrimetried by mercuric acetate in occurrence dithizon indicator;
2. Thiophene was determined according to the National State Standard 2706.5-95 based on interaction of thiophene with isatin with formation of solved in sulfuric acid indofenine with the following measurements of optical acid layer and determination of mass segment of thiophene по in graded diagram;
3. Sour sulfur was determined mathematically , as difference between total sulfur and thiophene sulfur.
Table 1.
Aproximed data of gas condensate sweetening.
|
S total
|
S thiophene
|
S sour
|
Primary gas condensate
|
0,4
|
0,19
|
0,21
|
After sweetening
|
0,083
|
0,08
|
0,003
|
Table 2.
Aproximed data of Petrol Fraction Gas Unvarying.
|
S total
|
S sour
|
S thiophene
|
Primary Gasolene Fraction Gas Unvarying sweetening
|
0,021
|
0,019
|
0,002
|
After sweetening
|
0,006
|
0,0041
|
0,0006
|
Tаble 3.
Aproximed data of fraction sweetening 200-360°С.
|
S total
|
S thiophene
|
S sour
|
Primary fraction 200-360°С
|
0,14
|
0,08
|
0,06
|
After sweetening
|
0,041
|
0,04
|
0,001
|
Table 4.
Series of experiences of oil sweetening.
General data of oil desulphuration.
№ sample
|
|
Total sulfur content % mas.
|
Sour sulfur content % mas.
|
Hydrogen sulfide content % mas.
|
Thiophene sulfur content % mas.
|
1
|
Composition of oil and sulfur gas condensate
|
0,64
|
0,0669
|
0,0011
|
0,372
|
2
|
Oil of sour type
|
1,615
|
0,0591
|
0,0057
|
0,4975
|
3
|
Typical oilstock
|
1,46
|
0,0253
|
0,029
|
1,4057
|
4
|
Typical oilstock
|
1,39
|
0,0109
|
missing
|
1,3791
|
5
|
Sample 1 after sweetening
|
0,2034
|
0,0002669
|
missing
|
0,1786
|
6
|
Sample 2 after sweetening
|
0,2618
|
0,003788
|
missing
|
0,2239
|
7
|
Sample 3 after sweetening
|
0,7754
|
0,00023
|
missing
|
0,7731
|
8
|
Sample 4 after sweetening
|
0,7595
|
0,0001
|
missing
|
0,7585
|
All 8 experiences, divided into series:
1. Series of control experiences;(1-4)
2. Series after pilot installation;(5-8)
As a result of carried out experiences was revealed, that lowering concentration of total sulfur specified predominantly on account of removal mercaptans.
On the grounds of the received data it is possible to confirm, that the given technology is applicable not only to sweetening of oil and gas condensate feedstock and products of their processing, but to gases as well, including natural.
What about existing technologies of desulfurization, proposed process has advantages (Table 5.):
1. Simplicity and compactness of technology on the basis of the processes fulfilled in the industry and devices, isn't present need of cardinal re-equipment of operating production, installation of catalytic cleaning of sulfur can be mounted in any technologically convenient place, possibility of application of technology as the main; and tertiary treatment of products after cleaning of sulfur;
2. The technology is applicable not only for purification of oil and gas condensates, but also for ready mercaptan containing products, by means of the mounting of independent lines sweetening, including oven – unit of sweetening – unit of condensation – unit of extracting disulphides – receiver of sweetening product;
3. Installation can be made any capacity, depending on capacity of the evaporating device or the furnace, in case of sulfur removal of finished products of primary distillation, and content of mercaptans in oil raw materials.
4. Capital expenditures for support sulphur removal of hydrocarbonaceous feedstock in case of the following running technological line of basic oil distillation sum 1% of total primecost of products, within terms of payback of the unit equals 2-3 months;
5. Little energy expenses for technological process support, following the actual technological chain;
6. Economic – lowering in 2-3 times the capacity of capital, exploitational expenses, the terms placing in operation.
Comparative charecteristics of the active technologies and technology of Limited Liability Company «Сompany «LN»».
Comparative rates
|
Active Technologies.
|
Technology of the «Сompany «LN»»
|
Hardware design
|
Adequately complicated, metal intensive. Requires optional equipment mounting
|
Simple diagram applicable in any technological diagram. Metall intensity is low.
|
Energy output.
|
Energy-intensive technologies
|
Energy charges of all kinds of resources are tiny.
|
Capacity of reagents
|
Great losses of reagents and expenses for its regeneration
|
Reagents expenses were lowered in 20-50 times.
|
Immensity
|
Practically nonrecoverable losses of the territory
|
Compact
|
Enviromental
|
Is accompanied by harmful emissions into atmosphere, drains, water losses
|
The quantity of set off pollution agents and expenses of resourses restricted to minimum.
|